01
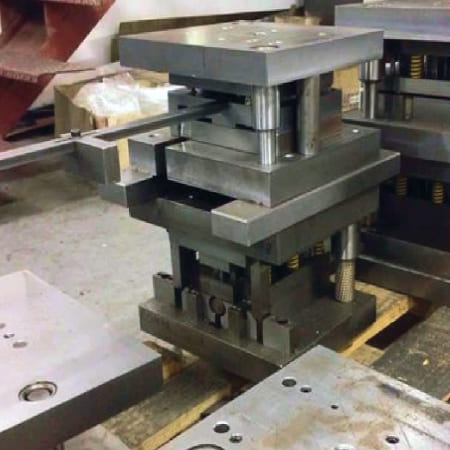
Tool Room
Our advanced tool room develops precise tools, calculating wax and metal contraction allowances for accurate dimensions.
We produce single and multi-cavity tools from durable aluminum, ensuring secure storage with clear identification.
02
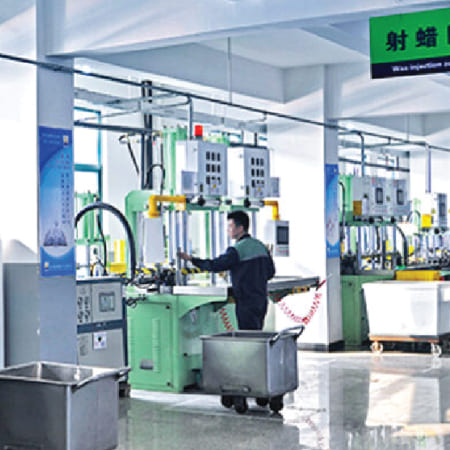
Wax Injection
Well-equipped setup with controlled atmospheric area.
We have Injection Machines with Auto Press, Semi-Auto Press, and Manual Press.
03
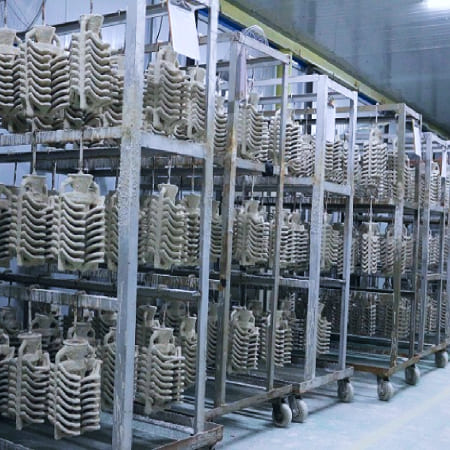
Shell Building
High-strength refractory materials are used after a thorough inspection.
Our facility features a rainfall sander, a high RPM slurry mixer, slurry drums, a fluidized bed, and high axial fans for optimal processing.
To maintain ideal temperature and humidity, we have installed de-humidity and a central air-conditioning system to maintain perfect temperature and humidity.
04
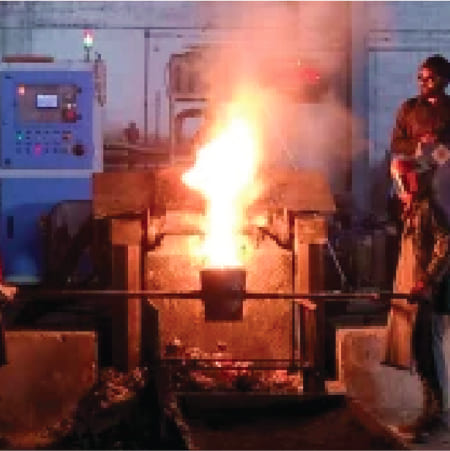
Melting
Induction furnace 250 kwh
Crucible capacity 300kg
Crucible capacity 100kg
Temperature of liquid metal measurement with pyrometer and controlled through temperature controller.
All equipment & temperature indicators and controllers are calibrated at regular intervals.
We used a t-spout ladle. The capacity of the ladke is 35kg, 50kg, and 80kg.
05
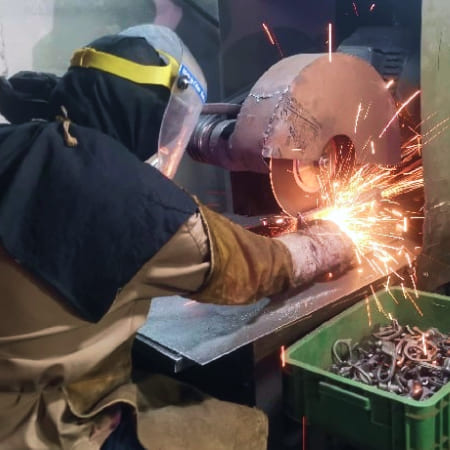
Fettling
Knockout Facility Lathe machine and Swing Grinding machine for Gate Machining.
Fiber Cutting and Pneumatic Grinding.
Shot Blasting Machine
-Rotary Table Type
Pickling and Passivation For Stainless Steel.
06
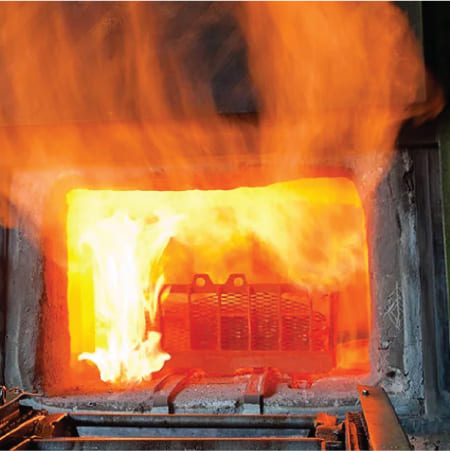
Heat Treatment
Furnace Details:
Fuel: Gas fire
Operating Temp: 1200° C
Calibration: API specification API-6D 25th Edition (Annx. H), API-6A (Annx. M) ASTM A991 (Volumetric Method)
Max Batch Capacity: 1000Kg
Thermocouples: 2 nos.
Agitation: Mechanical
Quenching Tank Capacity: 10000 Lt.
Max Quenching Time: 40 Sec.
07
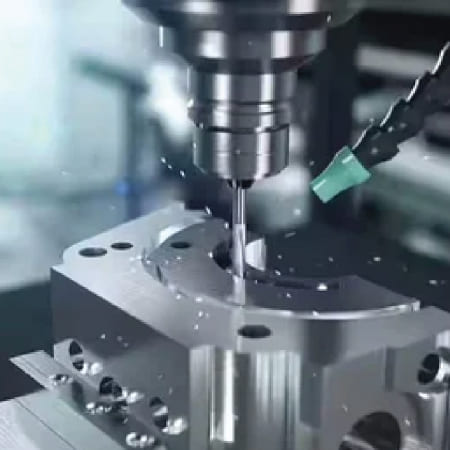
Machining
Castings are machined in-house using advanced CNC and VMC machines.
We offer outsourced facilities for HMC and VTL machines tailored to meet our customer's specific requirements.
This technology ensures precise dimensional accuracy and surface finish, meeting exact specifications outlined in customer drawings.
08
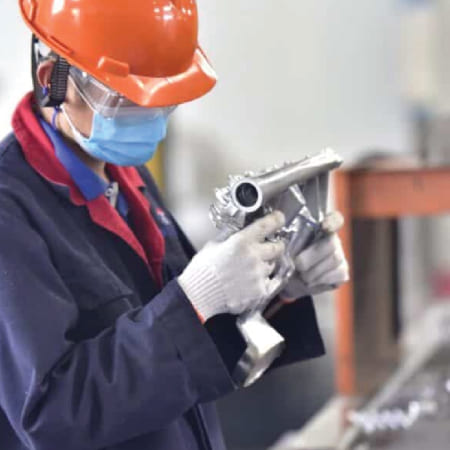
Inspection & Dispatch
Casting Inspected dimensionally to customer PO requirement.
Performed NDE and NDT Activity according to customer requirements.
Visual Inspection 100% Separate Location for Carbon Steel Casting & Stainless Steel Casting & other Alloys Packing According to Customer Specification.